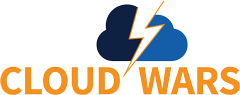
Over the last 30 years, cost has been a dominant force in supply chain design and management. Brick-and-mortar factories in the U.S. shut down, and production was moved offshore. Call centers and data entry facilities popped up in low-cost labor areas around the globe. Concepts like just-in-time manufacturing resulted in less inventory in the system overall, which lowered buffers everywhere.
These low-cost approaches continue to hum when everything works seamlessly. But add in a disruption of some sort — disease, weather, political, quality— and cracks start to show. There have been lots of industries where disruptions have resulted in shortages. Automotive, for example. Anything that uses computer chips. Medical supplies.
IBM has bucked the trend and, in so doing, stood out for its supply chain practices. By deploying a cognitive supply chain, IBM managed to maintain a 100% order fulfillment rate to its clients and reduce supply chain costs $160 million during this recent period of unprecedented disruption. How? With a cognitive supply chain.
What Is a Cognitive Supply Chain?
A cognitive supply chain leverages artificial intelligence (AI), machine learning (ML), and data analytics to enhance decision-making processes within the supply chain. It goes beyond traditional supply chain management by incorporating advanced technologies to create a self-learning and self-improving system. (Remember, one of machine learning’s cornerstones is that it improves over time.)
According to Ron Castro, vice president of IBM Supply Chain, “In the IBM cognitive supply chain, anyone can access the data depending on their authority. It’s a real-time, single view of the truth, giving us immediate insights to manage the client experience, operate with resilience, and react to market disruptions.”
Think of how powerful that is. Many individuals who’ve worked for large enterprises know the pain of operating multiple legacy systems, all maintained with different levels of diligence. If they could all see the same information, decision-making would be light years faster — and more effective.
Creating a Cognitive Supply Chain
The supply chain group assessed its processes and recognized that a lot of the required talent to create a cognitive supply chain was already under its own roof, in a separate division. IBM had significant efforts underway in AI, cloud computing, the Internet of Things (IoT), and other technologies. Consequently, it was able to utilize internal expertise to redesign its supply chain.
To accomplish that, IBM took eight specific actions:
- Consolidated Legacy Systems to a Single Source of Information. IBM virtually eliminated a reliance on offline spreadsheets.
- Fostered Data-Driven Decision-Making. IBM utilized advanced analytics tools to gather and analyze vast amounts of data from different stages of the supply chain. This data-driven approach enabled the company to identify inefficiencies, bottlenecks, and opportunities for improvement.
- Implemented Predictive Analytics. The use of predictive analytics allowed IBM to forecast demand more accurately, leading to reduced overstock and stockouts. This, in turn, minimized the costs associated with excess inventory and lost sales.
- Mitigated Risk. Cognitive supply chain technology helped IBM proactively identify and mitigate potential risks, such as supply disruptions or quality issues. This resulted in lower costs related to supply chain disruptions and product recalls.
- Collaborated with Suppliers. IBM fostered closer collaboration with its suppliers by sharing insights and data-driven forecasts. This collaboration led to more efficient production scheduling, reduced lead times, and lower procurement costs.
- Optimized Transportation. IBM optimized its transportation management system by implementing dynamic routing algorithms. This allowed the company to minimize transportation costs while ensuring timely delivery of products.
- Optimized Inventory. IBM adopted machine learning algorithms to continuously adjust inventory levels based on demand fluctuations. This reduced holding costs and freed up working capital.
- Acknowledged Culture Shift: Recognizing that the change in methods would be a huge cultural shift for IBM employees, the company invested in education and engagement to create enthusiasm and buy-in for the new ways of working.
As supply chain complexities continue to grow, organizations that embrace cognitive technologies and data-driven decision-making will be well-positioned to navigate the challenges of the future and drive sustainable cost savings.
IBM’s experience is not only a testament to its commitment to innovation but also a valuable lesson for businesses seeking to optimize their supply chain operations in an ever-changing landscape. By “walking the talk,” IBM is demonstrating to potential clients the immense potential for businesses to enhance their competitiveness and profitability. They reduced costs and improved supply chain reliability.
And $160 million in savings is worth paying attention to.
Gain insight into the way Bob Evans builds and updates the Cloud Wars Top 10 ranking, as well as how C-suite executives use the list to inform strategic cloud purchase decisions. That’s available exclusively through the Acceleration Economy Cloud Wars Top 10 Course.