Ivaldi is part of a profile series featuring startups participating in the Innovation Path at Cloud Wars Expo, taking place June 28-30 in San Francisco.
Who They Are
Ivaldi is a software supplier that aims to streamline the spare parts market for heavy industry by sending digital files, not parts, from place to place in response to customer requirements, so they can be produced on demand.
The company says its value proposition in migrating heavy industry to digital is threefold:
- It’s cheaper to build spare parts in exact quantities in response to customer orders than it is to maintain inventory.
- It’s more efficient to build as needed, reducing lead times.
- There’s less carbon emission in building products on-demand, closer to the end customer, than to ship large quantities from place to place.
“We’ve found that doing on-demand production of spare parts can reduce the carbon footprint of some parts by 90% compared to ordering from a centralized warehouse across the world,” says Alaina Piland, CFO of Ivaldi. The company envisions “A net-zero supply chain where the right parts are manufactured locally, saving time, cash, and carbon, while providing safe and durable parts.”
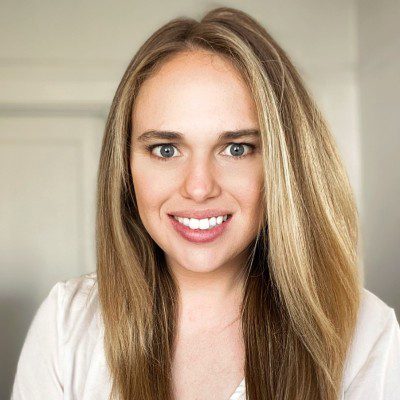
“Doing on-demand production of spare parts can reduce the carbon footprint of some parts by 90% compared to ordering from a centralized warehouse across the world.”
Alaina Piland, CFO of Ivaldi
The company is based in San Leandro, California. It has 18 employees, just under $9 million in venture capital funding, and it’s part of the sap.io accelerator program.
What They Do
Ivaldi has a straightforward value proposition: Rather than absorb the costs of maintaining inventory and transportation, maintain a digital inventory and manufacture spare parts on demand. This approach can eliminate rental or mortgage costs for warehouses while implementing a just-in-time system for building and delivering parts – all managed on a digital basis.
Ivalid’s digital warehouse system gives companies access to:
- Digitized parts
- Analysis and recommendations of not only what parts could be printed, but what parts should be printed
- A set of variables that can be adjusted based on customer priorities, such as the prioritization between time, cost, and carbon footprint
- An on-demand network of certified 3-D print sources
- Material-Technology-Location Comparison — this product feature provides an overview of the available technology and materials a customer has, based on location, giving customers the ability to determine which manufacturing networks are available to produce a given part at the required time.
The company encourages its customers to use one of several on-demand approaches to building products: 3D printing, injection molding, or CNC milling.
Through the company’s selection, digitization, and documentation process, every part goes through quality control, physical, and algorithmic verification. All the documentation necessary to manufacturing, design, and performance requirements is stored in what Ivaldi calls an “envelope.”
“On-demand production technologies are getting faster, better, and cheaper, and we can use that to help solve supply chain problems,” Piland says, noting that the global aftermarket for spare parts is valued at $80 billion, so there’s a massive opportunity to apply automation to make that aftermarket function more efficiently. Today’s supply chains for these products are slow, fragile, costly, and carbon-intensive, she adds.
The typical Ivaldi customer is a user of SAP’s S4 Hana Cloud.
Who They’ve Impacted
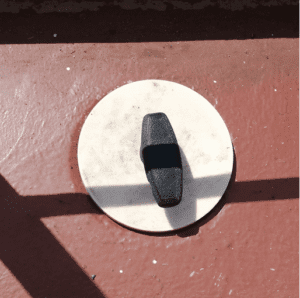
An unnamed Ivaldi customer is a manufacturer of scupper plugs. A scupper plug (pictured, above) is a widely used item that closes drainage holes on open decks in the maritime industry. Each plug has a unique design, but every one has an expandable element that plugs a hole. The classic scupper plug design has brass tops and discs on the bottom.
Conventional scupper plugs are expensive and an easy target for theft because brass components can be quickly sold on the black market. The rubber element is prone to aging and frequently needs to be replaced. Although they look similar, there are small differences between manufacturers that prevent them from being interchangeable.
By applying digital warehousing and manufacturing via 3D printing, the scupper plugs are as functional as traditional versions but they become faster and easier to procure. Since only the exact number required is produced, this reduces costs and environmental impact.
Closing Thoughts
Ivaldi has an updated spin on just-in-time manufacturing, optimized for a time when companies are laser-focused on sustainability, struggling with fragile supply chains, and under extreme cost pressures due to inflation.
It will be fascinating to monitor uptake of the company’s technology as prospective customers in heavy manufacturing search for ways to lower their costs and make their supply chains more flexible and resilient. Those are desperately needed improvements, and Ivaldi has answers to help make them reality.
Want to gain more insights from Cloud Wars Expo?
Starting on July 20th, more than 40 hours of on-demand cloud education content will be available for free to Acceleration Economy Subscribers.
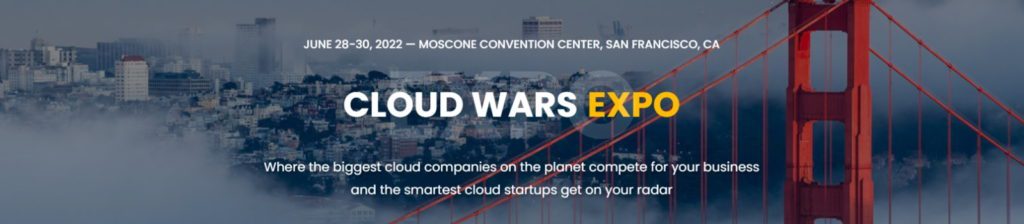